Maintaining quarry crushers is crucial for ensuring the efficiency and longevity of quarry operations. Proper maintenance practices not only enhance equipment reliability but also contribute to worker safety and environmental sustainability. This article explores essential best practices that quarry operators should follow to optimize crusher performance and minimize downtime.
The Importance of Regular Maintenance
Regular maintenance is the cornerstone of efficient quarry operations, particularly when it comes to crushers. These heavy-duty machines are subjected to intense wear and tear, processing hard rocks and minerals day in and day out. Neglecting maintenance can lead to costly breakdowns, production delays, and safety hazards. Implementing a proactive maintenance strategy ensures that stone crusher quarry operate at peak performance, maximizing productivity and profitability.
Inspections and Scheduled Checks
Regular inspections are vital for identifying potential issues before they escalate into major problems. Scheduled checks should include examination of wear parts such as liners, jaws, and hammers for signs of wear and damage. Inspecting hydraulic systems, lubrication levels, and electrical components ensures all systems are functioning optimally. This proactive approach allows maintenance teams to replace worn parts and address minor issues promptly, minimizing unplanned downtime.Implementing Preventive Maintenance Programs
Preventive maintenance programs are proactive strategies designed to prevent equipment failures before they occur. These programs typically involve routine tasks such as lubrication, fluid checks, and component replacements based on manufacturer recommendations and operational conditions. By adhering to a preventive maintenance schedule, quarry operators can extend the lifespan of crushers, reduce repair costs, and maintain consistent production levels.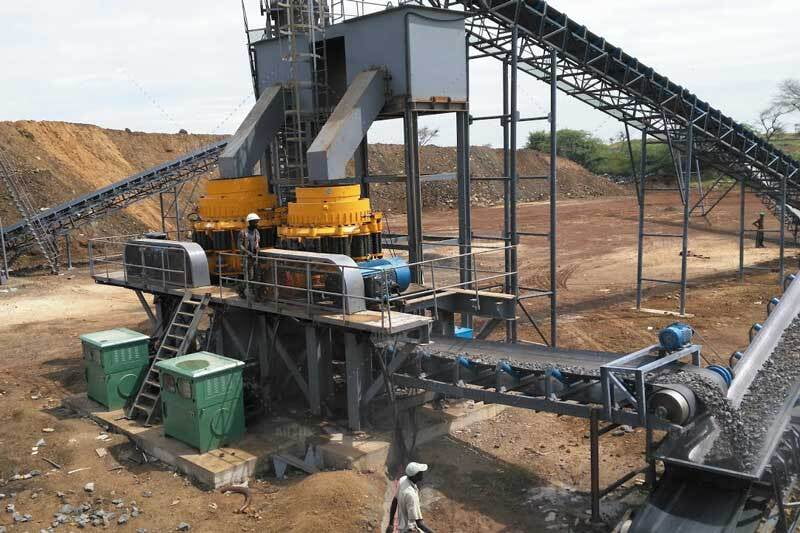
Optimizing Crusher Performance
Maximizing crusher performance involves more than just maintenance; it requires careful attention to operational practices and efficiency improvements. Proper operation not only enhances productivity but also ensures that limestone crushers operate within safe limits and comply with environmental regulations.
Adjusting Crusher Settings for Optimal Performance
Crusher settings play a crucial role in determining the quality and quantity of output material. Operators should regularly adjust crusher settings such as closed-side setting (CSS) and eccentric speed to achieve desired product sizes and maximize throughput. Monitoring these settings and making adjustments based on feed material characteristics and production requirements can optimize crusher efficiency and reduce energy consumption.Utilizing Advanced Monitoring and Control Systems
Advanced monitoring and control systems provide real-time data on crusher performance, allowing operators to make informed decisions. These systems monitor parameters such as crusher load, power draw, and cavity level, providing insights into operational efficiency and potential issues. Integrating automation technologies enables remote monitoring and adjustment of crusher settings, enhancing safety and efficiency while reducing the need for manual intervention.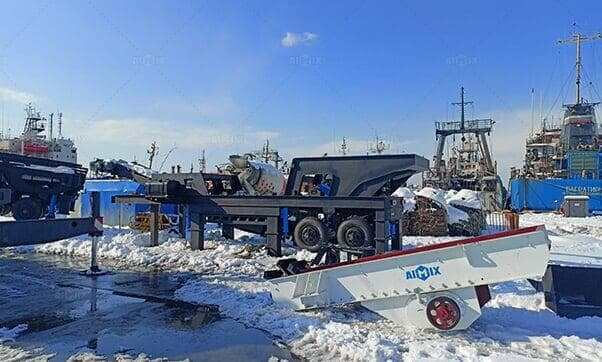
Ensuring Safety and Compliance
Safety is paramount in quarry operations, particularly when working with crushers and heavy machinery. Implementing robust safety protocols and ensuring compliance with industry standards and regulations are essential for protecting workers and maintaining a safe working environment.