Granite crushing plants play a crucial role in supplying aggregates for construction projects, adapting continuously to meet the industry's changing demands. This article explores how innovations in equipment and technology, efficiency enhancements in operations, and strict adherence to safety and environmental standards ensure these plants remain at the forefront of the construction industry.
1. Innovations in Equipment and Technology
Granite crushing plants are leveraging cutting-edge equipment and technology to enhance productivity and efficiency in aggregate production.
Advanced Crushers and Screens
Incorporating state-of-the-art crushers and screens is essential for maximizing throughput and achieving uniform product sizes in granite crushing plants. High-capacity cone crushers and impact mobile crusher equipped with advanced features such as hydraulic settings adjustment and high-efficiency screening decks ensure optimal performance and versatility in processing various grades of granite.
Automation and Remote Monitoring
The integration of automation systems allows granite crushing plants to operate with precision and consistency. Automated controls for crusher settings, conveyor speed adjustments, and real-time monitoring of equipment performance enable operators to optimize production levels while minimizing energy consumption and operational costs. Remote monitoring capabilities further enhance operational efficiency by enabling proactive maintenance and troubleshooting from off-site locations.
Sustainable Crushing Practices
Modern granite crushing plants prioritize sustainability by implementing practices that reduce environmental impact and promote resource efficiency. Utilizing energy-efficient crushers, employing dust suppression systems, and adopting water recycling techniques are integral to minimizing the plant's carbon footprint. By embracing sustainable crushing practices, these plants contribute to environmental stewardship and align with industry-wide sustainability goals.
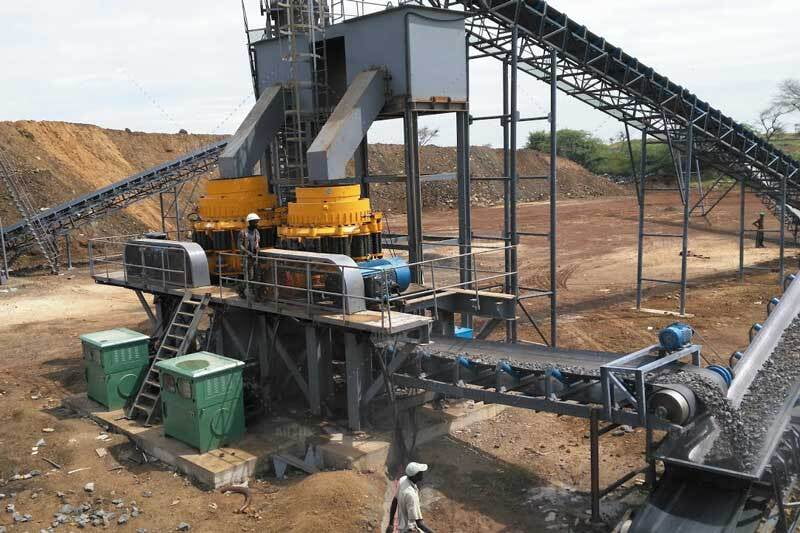
2. Efficiency Enhancements in Operations
Efficient operations are key to the success of granite crushing plants, ensuring seamless material flow and maximizing production output.
Optimal Material Handling Techniques
Effective material handling techniques are critical for maintaining continuous operation in granite crushing plants. Utilizing conveyors, loaders, and stackers optimizes the movement of raw materials, reducing bottlenecks and enhancing productivity. Strategic placement of equipment and stockpiles minimizes material handling distances, streamlining workflows and minimizing operational downtime.
Streamlined Workflow Integration
Granite crushing plants integrate workflows to streamline production processes and enhance efficiency across multiple stages of aggregate production. From primary crushing to final screening, seamless integration of crushers, screens, and conveyors ensures a cohesive operation that meets production targets and quality standards. Efficient workflow integration facilitates rapid material processing and delivery, supporting timely project completion and customer satisfaction.
Maintenance Strategies for High Uptime
Proactive maintenance strategies are essential for maximizing uptime and prolonging the lifespan of equipment in granite crushing plant. Scheduled inspections, routine maintenance tasks, and predictive maintenance techniques prevent equipment failures and minimize unplanned downtime. Regular lubrication, component replacements, and monitoring of wear patterns ensure crushers and associated machinery operate at peak performance levels, supporting continuous production and operational reliability.
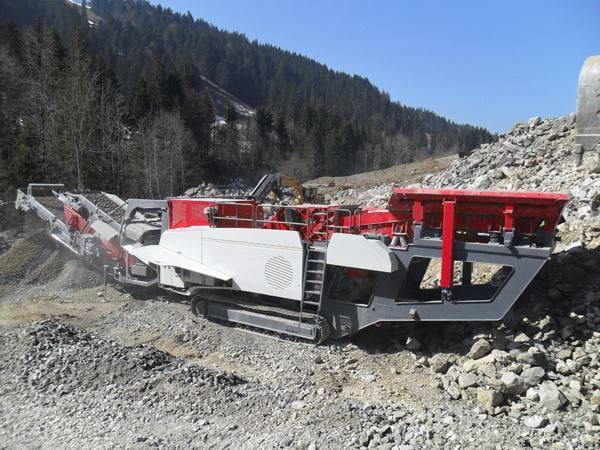
3. Meeting Safety and Environmental Standards
Granite crushing plants prioritize safety and environmental compliance to protect personnel and minimize ecological impact.
Rigorous Safety Protocols
Implementing rigorous safety protocols is paramount to safeguarding workers and maintaining a secure operating environment in granite crushing plants. Comprehensive safety training programs, hazard assessments, and the use of personal protective equipment (PPE) mitigate risks associated with equipment operation and material handling. Safety audits and regular safety meetings reinforce adherence to safety protocols and foster a culture of safety excellence among plant personnel.
Environmental Impact Mitigation
Mitigating environmental impact is a priority for granite crushing plants, which implement measures to minimize air, water, and noise pollution. Dust suppression systems, enclosed conveyor systems, and vegetation barriers reduce airborne particulates and noise emissions, promoting environmental stewardship and regulatory compliance. Water management practices, including recycling and runoff containment, preserve natural resources and support sustainable operations within the local ecosystem. AIMIX equipment has been equipped with advanced technology to ensure environmental friendly.
Compliance with Regulations
Granite crushing plants adhere to stringent regulatory requirements governing environmental protection, workplace safety, and operational standards. Compliance with local, state, and federal regulations ensures legal compliance and demonstrates commitment to responsible business practices. Regular environmental audits, permits, and reporting obligations facilitate transparency and accountability, fostering trust with regulatory authorities and stakeholders.
In conclusion, granite crushing plants adapt to the evolving needs of the construction industry by embracing technological innovations, enhancing operational efficiency, and prioritizing safety and environmental responsibility. By integrating advanced equipment, optimizing workflows, and complying with regulatory standards, these plants sustainably meet the demand for high-quality aggregates while minimizing environmental impact and promoting industry-leading practices.